Quality Assurance Services
We are dedicated to quality and care.
We offer our team of qualified inspectors to serve your company.
ACE Services Group Inc. offers a quality inspection package service to ensure your products are up to company standards and specifications. We specialize in Third Party Sorting services, including CS1 and CS2. Our thorough sorting and inspection services extend to daily and weekly quality reports and I-charts.
We offer high-quality sorting and inspection services for competitive manufacturing companies. We send our clients qualified inspectors for a number of various tasks.
Our services include (see details below the list):
- Inspecting/Sorting
- Third party containment – CS1, CS2
- Gauging
- Barcode Error Proofing
- Reworking
- Repackaging
- Tracability
Our team of inspectors follows a professional and thorough procedure that ensures quality and efficiency for your company. We offer competitive hourly rates for your needs, whether it is sorting and inspecting for measurement to handling a wide range of materials.
Quality Assurance Solutions
Making sure your products are up to the standards and quality your company deserves can be a difficult task to maintain without the right people. However, our employees at ACE can greatly save unexpected costs in defects by following a thorough procedure to ensures your products meet your specifications and standards:
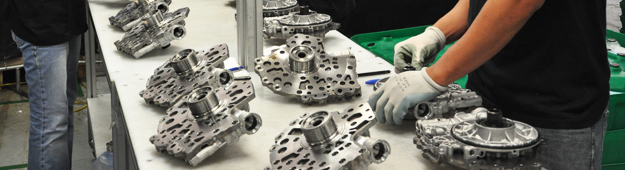
Pre-shipment Inspection (PSI): Each product is checked for uniform control before they leave the manufacturer based on the company’s criteria and specifications.
During Production Inspection (DUPRO): Products are inspected for control and recommendations while the manufacturing process occurs.
Initial Production Check (IPC): Machinery and materials are inspected to ensure quality and safety early in the manufacturing process to ensure the company's standards and recommendations are being met.
Container Loading Checks (CLC): A final inspection of products makes sure they are up to quality and standards before they are loaded for shipment.
End of the Line Inspection: This type of inspection is important to ensure the products of each production line meets the required quality level before they are transferred to the next lines.
Visual Inspection: Sorting of products using the human senses, such as vision, hearing, touch, smell.
Final Inspection: Between the transport of product from the manufacturer to the supplier, we can step in to aid in the final inspection with the quality requirements set by either side. We are able to relocate our inspectors for on-site final inspection or off-site final inspection at our location.
What is Controlled Shipping/Containment?
Controlled Shipping is a root-cause problem solving process that sorts for non-conforming products/materials from a manufacturer. When a customer receives a great number of non-conforming parts from the supplier, the supplier is immediately contacted to be notified of the required Controlled Shipping. This requires the supplier to include a redundant inspection process on top of their current control process in order to isolate defects and find ways to prevent future errors in production.
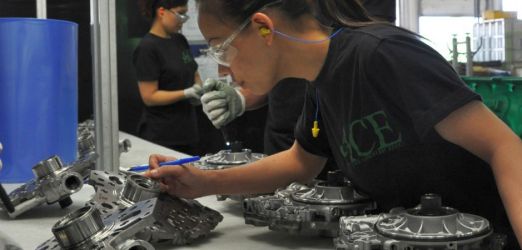
ACE Services Group Inc. can step in at any time to send a team of qualified inspectors to help you exit both levels of Controlled Shipping (CS1 and CS2). We will send our employees promptly onsite or offsite to help your company compete for any level of containment.
There are two levels of the Controlled Shipping process: CS1 and CS2
Controlled Shipping - Level 1 (CS1) – CS1 requires for the supplier to perform a redundant inspection check. ACE Services Group Inc. is able to offer our team of inspectors to travel onsite or offsite to help you exit containment with care and efficiency.
Controlled Shipping – Level 2 (CS2) - Suppliers must undergo CS2 when they have failed to correct their quality issues in CS1 or when there is still a majority of quality issues evident. ACE Services Group Inc. will send our inspection team promptly onsite or offsite to help your company complete this level of containment.
Full documentation (I-Charts, Sorting Reports, etc.) is available in our inspection services for your needs.
What is Controlled Shipping/Containment?
ACE Services Group Inc. provides employees to rework and repair non-conforming materials and products in order for them to be accepted by your customer. We can send workers to your facility or the customer’s facility to bring these products back to conformity.
With the use of onsite or offsite tools and equipment, we apply our values in care and efficiency to help you maximize the materials sent for production.
ACE Services Group Inc. can step in at any time to send a team of qualified inspectors to help you exit both levels of Controlled Shipping (CS1 and CS2). We will send our employees promptly onsite or offsite to help your company complete any level of containment.
There are two levels of the Controlled Shipping process: CS1 and CS2
Controlled Shipping - Level 1 (CS1) – CS1 requires for the supplier to perform a redundant inspection check. ACE Services Group Inc. is able to offer our team of inspectors to travel onsite or offsite to help you exit containment with care and efficiency.
Controlled Shipping – Level 2 (CS2) - Suppliers must undergo CS2 when they have failed to correct their quality issues in CS1 or when there is still a majority of quality issues evident. ACE Services Group Inc. will send our inspection team promptly onsite or offsite to help your company complete this level of containment.
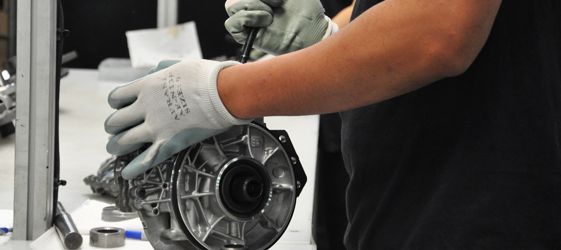
Full documentation (I-Charts, Sorting Reports, etc.) is available in our inspection services for your needs.
What is Controlled Shipping/Containment?
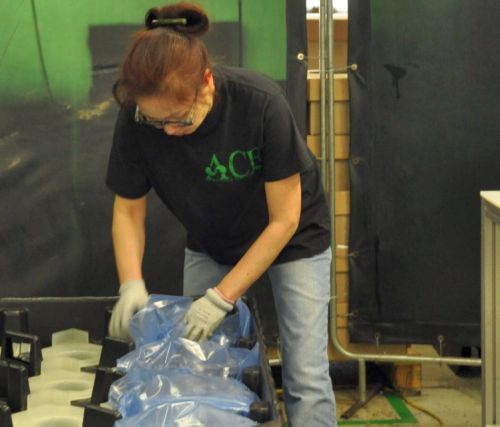
Our repackaging team ensures that each package of the manufacturer's product is secured and meets quality standards.
We offer repackaging services onsite, offsite or at our warehouse location.
Receive shipment, we call instant communication, real-time or email, or phone to notify customer that something is wrong or different, send copies of shipment papers to notify of the shipment arrival.
Next day sorting report with serial numbers, lot numbers, or custom requests like package number, I chart, Track sort, Client portal.
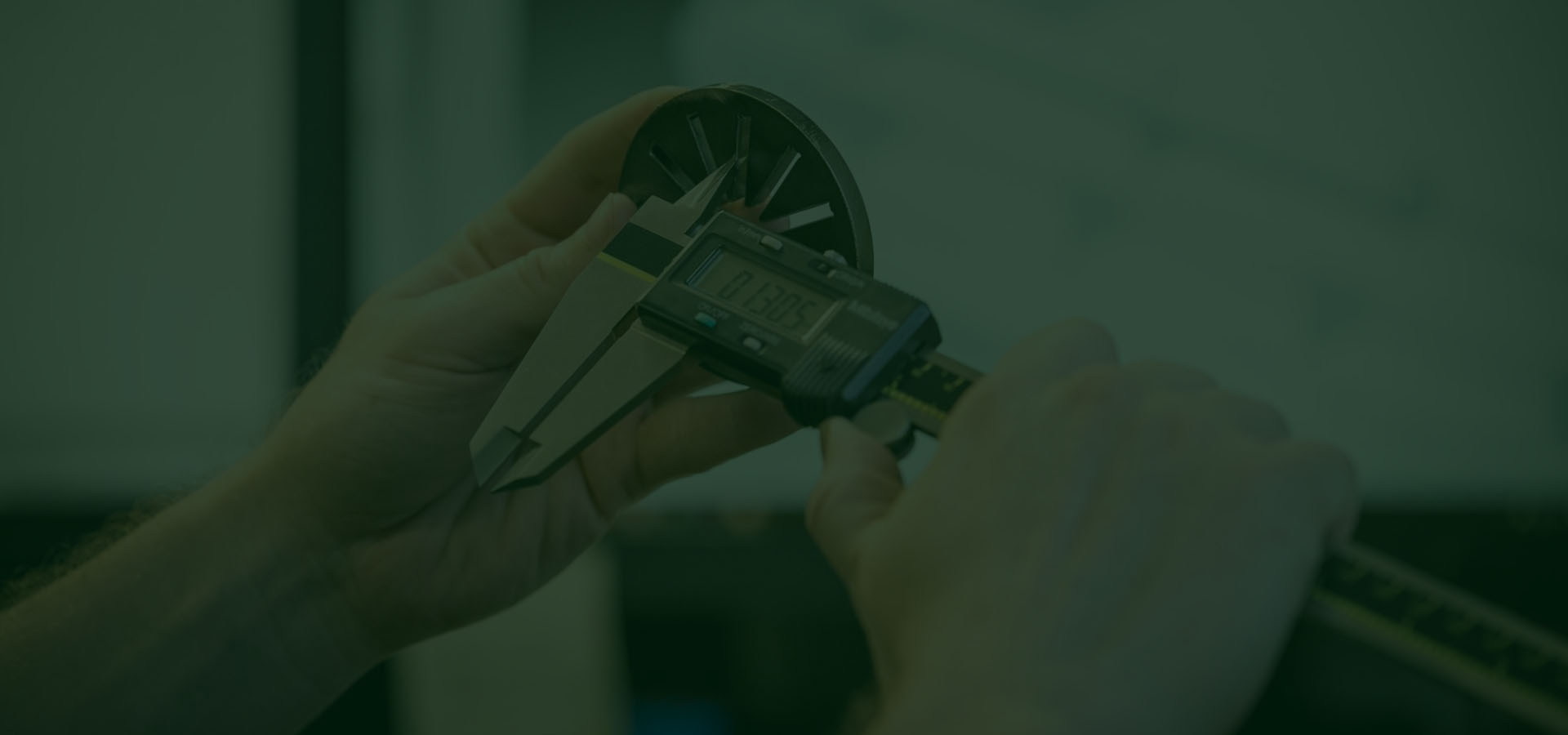